
Inspiration Takes the Wheel
Lacks engineering advancements empower design versatility beyond the expected
Lacks history of breakthroughs in surface finish technologies and improvements in engineering design have produced wheel assembly and component solutions that allow designers the freedom to imagine outside traditional restraints. We continue to strive to provide improvements in engineering and design like weight reduction, aerodynamic efficiency, and advanced 3-D texturing capabilities. With Lacks, precision design capabilities founded on engineering innovations makes realizing a particular vision—or even encouraging the formation of new ideas—the norm.

Reinvent Your Wheel
Lacks applications open up a world of design possibilities
From completely original surface designs to XPOSE® technology insert systems on existing wheels, Lacks wheel trim composite applications offer a wide range of wheel options to fit your engineering and design needs. Our technologies allow a single backbone to accommodate a number of designs without altering the engineering standards. By separating design from the wheel structure, design restraints may be eliminated, trim-level differentiation is simple, and the wheel life cycle is extended. Mass reduction and advancements in aerodynamic performance offer fuel-economy savings without sacrificing design or functionality.
Anatomy of a light weight
composite wheel
Chromtec®
Chromtec® is a full composite design surface permanently bonded to a wheel structure
- A range of style options on the same validated wheel structure reduces tooling and testing costs, extending vehicle life cycle management
- By simply changing the finish Lacks Wheel Trim System technology can extend the life of the wheel—making refreshing/trim level differentiation intuitive
- A range of finish and texture options presents a rich and compelling array of design opportunities
- Composite wheel construction ensures design freedom independent of mass and stiffness targets
Xpose® Single-Piece
Insert Wheel Assembly
Xpose® single-piece composites
Xpose® single-piece partial composites design surface enhances underlying visible wheel structure
XPOSE® inserts increase design potential and versatility of a visible wheel backbone. With finish and texture variability, XPOSE® improves design capability adding finish contrast options, spoke variations, and aerodynamic applications to a validated wheel backbone.
Xpose® Multipiece Insert
Wheel Assembly
Xpose® Multipiece Composites
Xpose® multipiece partial composites multiply the design potential of a visible wheel backbone
XPOSE® inserts enhance the finish capabilities available through unmatched flexibility. Insert and backbone interaction options expand design potential and add complexity to the design story.
Why XPOSE® partial composite inserts?
- Provides best-in-class fit and finish through gap control and accurate location of insert technology to the wheel assembly, resulting in fewer field issues such as BSRs
- High quality, solid feel than mechanically fastened inserts
- Extends wheel life cycle with increased refreshibility and shorter design cycles
eVolve®
Lacks composite wheel design flexibility can enhance wheel surface aerodynamic optimization potential. Coupled with inherent weight-saving characteristics, Lacks eVolve® wheel technology contributes to improved fuel economy and a lower carbon footprint
- Minimizes weight and has the potential to improve aerodynamics, the key to better fuel economy
- Lighter weight backbone yields a lower backbone wheel cost
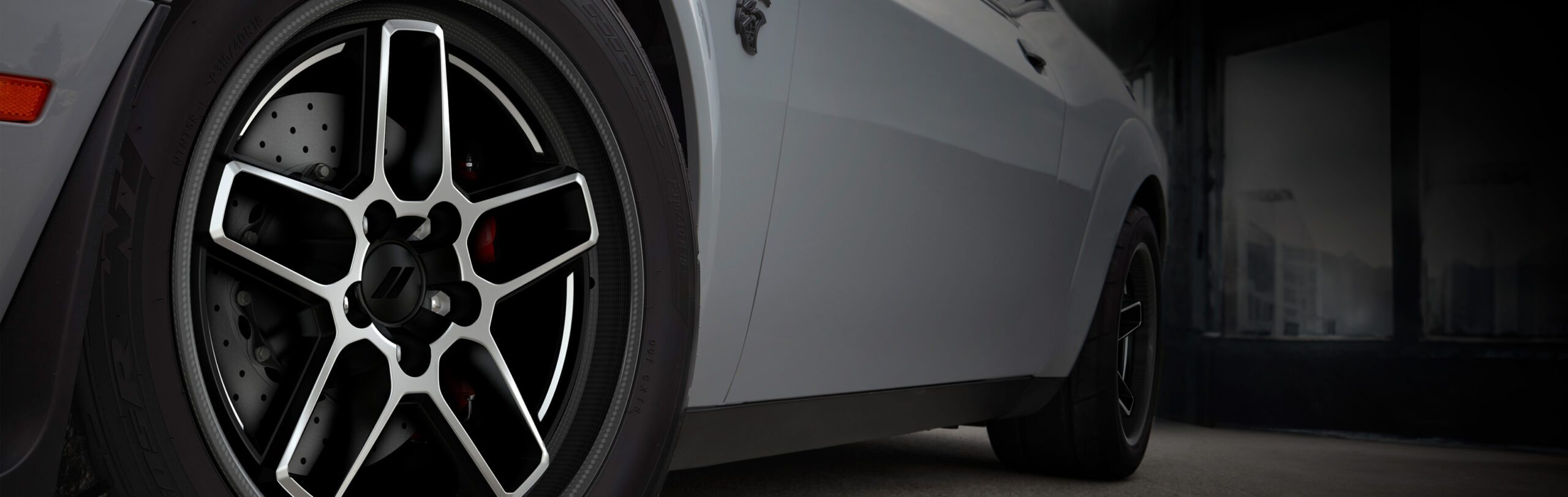
INTRODUCING LACKS CARBON FIBER WHEELS
FASTER. LIGHTER. STRONGER.
Unlock the performance possibility of carbon composites with our new 2-piece carbon fiber composite wheels.
CARBON FIBER WHEELSWhy Lacks Wheel Trim Systems?
- Composite design surfaces weigh less than traditional steel or aluminum without sacrificing strength
- End-to-end manufacturing control and Lacks finish technologies make trim level differentiation seamless
- Technical capabilities including sculpted bright surfaces, minimal radii and tight sidewall draft tolerances mean fewer limits and more possibilities for adding dimension to wheel design
- Over 36 million wheels in the field over 20 years